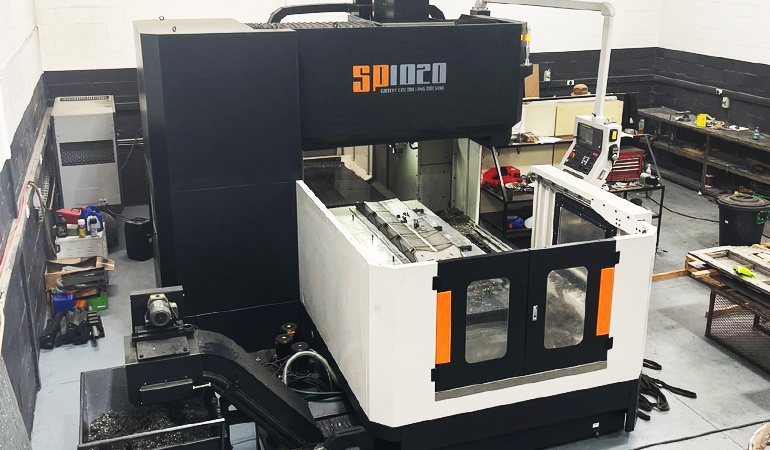
Lead Machine Tools recently installed another Sino SP1020 Double Column Machining Center.
Larger parts require larger capacity and increased rigidity in order to support heavier table loads. SINO'S Bridgecenter Double Column Machining Centers are designed for extreme cutting capacity, offering the benefits of solid box way construction, high speed/high torque spindle options, spacious work envelopes, and a patented double column bridge type design. Standard roller linear slideway and #40 and #50 taper spindle configurations make these machines ideal for the mold industry where high levels of accuracy are needed in roughing & finishing large cavities and cores.
Spindle
-Belt type spindle is economic, it is with pneumatic tool clamping and unclamping.
-Gear head type is with higher rigidity, better for heavy cutting compared with belt type.
-For direct driven, spindle motor directly connects to spindle through high quality high torque high rigidity MAYR carbon fiber coupling (Tks=975Nm), which helps to fulfill the nice performance of main motor as overturn torque is much reduced.
Counter weight system (Double hydraulic cylinders)
-Z axis with balance counterweight system ( double balance cylinder + hydraulic station ) to improve Z axis stability and positioning accuracy.
-Hydraulic station not only provide power source for balance cylinder, but also for tool clamping and unclamping.
-Double balance cylinder can efficiently decrease bending moment during Z axis movement.
3 axes driving
-The ball screws are directly coupled to the servo motor. It will express mostly motor performance and improve machine accuracy and efficiency.
-10 years free service reducer STOBER in X \Z axes (Germany brand).
Spindle box
-With large cross section design, it improve spindle box rigidity by 20% compared with other competitors.
-SINO spindle box thickness is 345mm, usually competitors’ is just 60mm.
Saddle
-To improve saddle rigidity and anti-shock, Â Z axis is made of box guideway with plastic which is manually scraped well.
-One piece of screw nut seat and saddle to improve machine accuracy.
Beam
-Ladder designed beam assured spindle case gravity backward.
-Reasonable distance between guideway to spindle center by FEA.
Base
-Foundation hole keep in vertical line with linear guideway which assure a better loading support.
-If machine is installed by two holes, one fixing hole and one adjusting hole, the machine base is easily deformed due to unequal force.
-Trapezoid foundation hole ensure machine stability.
-500mm distance between two holes keep reasonable equal force.